平準化
Heijunka (Production Leveling)
定義:
生産量や生産する品種の順番を、一定期間(例えば1日や1週間)で均等にならすことです。需要の変動があっても、最終組み立てラインには少量ずつ、ミックスされた品種が流れるように計画します。
目的:
生産ラインの負荷を安定させ、ムダ(作りすぎ、手待ち)やムラ(ばらつき)、ムリをなくすことです。ロットサイズの縮小や段取り時間の短縮(SMED)とセットで行われることが多いです。
補足:
OTRS10は、各工程のサイクルタイムや段取り時間を正確に把握・分析し、さらに山積み表などでラインの負荷バランスを視覚化できます。これらのデータは、生産計画の平準化が可能か、あるいは平準化計画に対して現場が対応できているか(例:段取り時間の問題で品種切り替えに時間がかかり平準化が崩れる)を評価する上で有用な情報となります。
平準化生産とは?
生産における平準化は、「量」・「種類」を均等にばらして生産する手法の一つです。
平準化生産は、いつでも一定に生産量や生産品目が流れ続けている状態です。トヨタ生産方式のジャストインタイムは平準化生産ができていることが前提です。
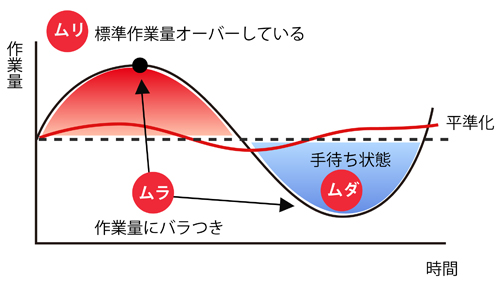
平準化生産はロット生産と対比されます。一般的なロット生産ではまとめてロット化するためラインの効率がよく、段取り回数も少なくなります。反面、最大生産数量に合わせて人と設備が用意されるため、生産数量が最大でないときに、手待ちのムダが発生します。今日は10個生産、明日は100個生産といった具合に生産計画にばらつきが起き、在庫が増えたり、逆に欠品が生じ、結果的に多くのムダを含む原価の高い品目になります。
平準化生産では、生産量と種類が一定なので、前後工程の在庫が抑えられ、お客の急な要求にも対応しやすくなります。
生産のムダを取り除き、原価低減を進めるための生産現場方法として平準化生産は重要ですが、 段取替の回数が増えるというデメリットもあるので、回数と時間を改善して効率化をすすめる必要があります。
平準化をすすめる手順としては、生産数量と品目の分析を行い、数量の多いものから平準化していきます。また、前後工程の関連性を明確にし、整流化をすすめ、ABC分析やロットサイズの最小化を考えながら平準化計画のサイクルを決めていきます。